Heat Treatment Services
Heat treatment is the process of enhancing the hardness, ductility and fatigue resistance of a material through precise temperature control and professional processing, providing customers with high-quality custom metal parts that meet specific performance requirements.
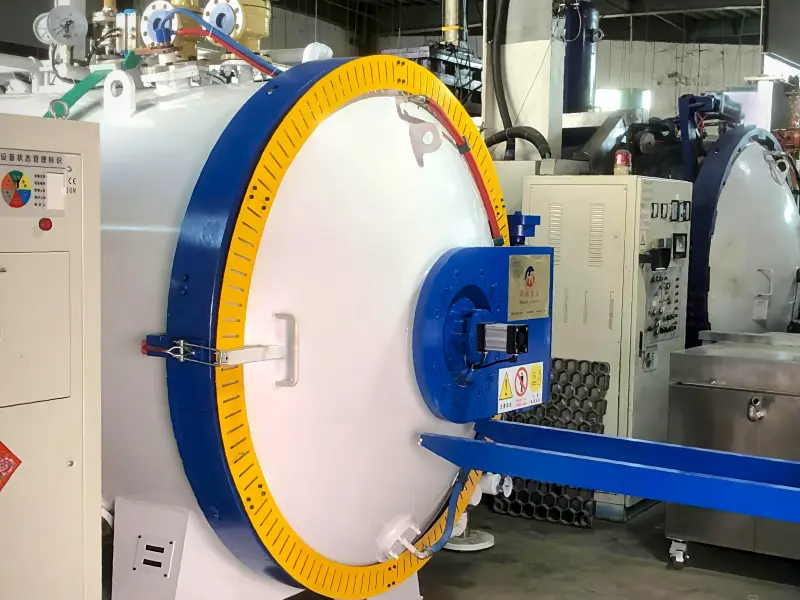
Common Types of Heat Treatment
FastPreci ensures that your CNC machining custom parts have excellent performance by applying the suitable heat treatment to the material based on the part structure and application as well as your requests.
Annealing
Annealing involves heating a metal, usually steel, to a temperature abzove its recrystallization point, which allows its crystalline structure to reform with reduced internal stress. The material is held at this temperature to allow sufficient diffusion of atoms, promoting the formation of a softer, more ductile phase. Then, it is cooled slowly—often within the furnace—to avoid introducing stress. This controlled cooling refines grain structure, minimizes hardness, and enhances ductility, making the metal easier to machine, shape, or form without cracking.
Normalizing
In the normalizing process, steel is heated to a temperature slightly above its critical transformation range to fully austenitize it, then allowed to cool in open air. This faster cooling rate compared to annealing produces a finer, more homogeneous pearlitic or ferritic microstructure. The result is improved toughness, strength, and wear resistance, with reduced brittleness. Normalized parts have a uniform, small-grain structure, which enhances consistency in mechanical properties and is beneficial for components subjected to impact and stress.
Quenching
Quenching rapidly cools a material—typically steel—after heating it above its austenitizing temperature, locking in a hard martensitic structure. The process involves immersing the heated material in a cooling medium, like oil, water, or polymer solutions, to bring down its temperature quickly. This fast cooling traps carbon atoms within the lattice, creating a supersaturated, high-hardness structure that greatly increases strength and wear resistance. However, the quenching process introduces internal stresses, making the material more brittle, so additional tempering is often required to balance hardness with ductility.
Tempering
Tempering is used to adjust the hardness and reduce the brittleness of a quenched metal, particularly martensitic steels. The quenched metal is reheated to a temperature below its critical transformation point and held for a specific duration, then cooled. This controlled heating allows partial diffusion of carbon atoms, relieving internal stresses and refining the microstructure. Tempering increases toughness and improves resistance to cracking, while retaining much of the strength gained through quenching, making it suitable for high-strength applications.
Surface Hardening
Surface hardening processes, such as carburizing, nitriding, and induction hardening, are designed to increase the hardness of a material’s surface while maintaining a tough, ductile core. In carburizing and nitriding, the surface is enriched with carbon or nitrogen, which penetrates the outer layer and forms a hardened case when exposed to controlled heat. Induction hardening, meanwhile, involves rapidly heating the surface with electromagnetic induction followed by quenching. Surface hardening is ideal for parts that require high wear resistance on the surface—such as gears and camshafts—while needing a ductile core to absorb impact.
Aging
Aging, particularly in precipitation-hardenable alloys (e.g., aluminum and titanium alloys), involves heating the alloy to an elevated temperature to allow for controlled precipitation of secondary phases. This phase separation creates obstacles within the grain structure, increasing hardness and strength through precipitation hardening. The aging process can be natural (occurring at room temperature) or artificial (accelerated by heating). The result is a significant improvement in mechanical properties, such as tensile strength and stability, making aged alloys well-suited for structural components in demanding applications like aerospace and automotive manufacturing.