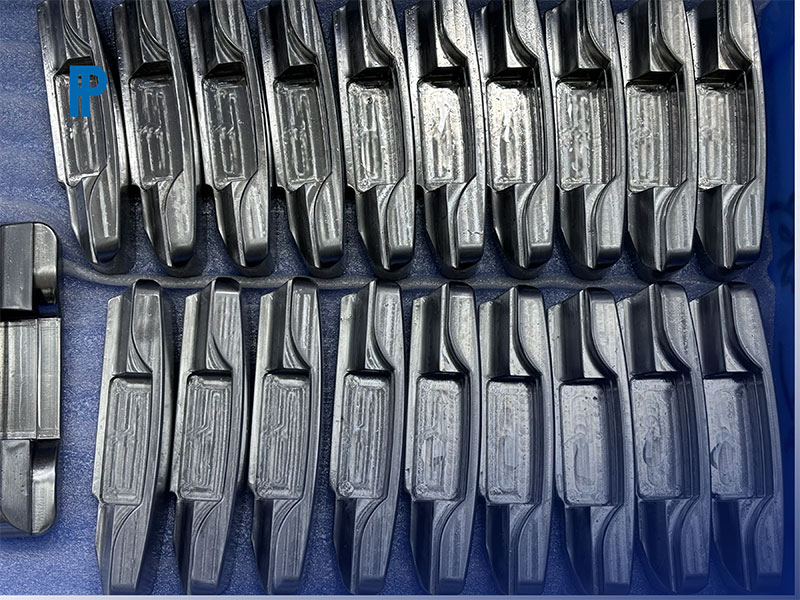
Characteristics of metal materials
1. High strength and rigidity
Metal materials usually have very high tensile and compressive strength. For example, the tensile strength of stainless steel ranges from 500-750 MPa, while the tensile strength of titanium alloys can be as high as 1,000 MPa or more, making them excellent in the manufacture of structural and load-bearing parts. In CNC machining, the strength of the metal makes the finished product more durable and adaptable to harsh working environments.
2. Thermal and Electrical Conductivity
Most metal materials have good thermal conductivity, for example, aluminum has a thermal conductivity of up to 237W/(m-K) and copper has an even higher thermal conductivity of 401W/(m-K). Therefore, aluminum and copper are widely used in electronics, heat dissipation and other industries. In addition, the conductivity of the metal also makes it a core material for electrical and electronic equipment, for example, in the battery cooling system of electric vehicles, aluminum and copper are widely used because of their excellent electrical and thermal conductivity.
3. Corrosion resistance
Stainless steel and titanium materials are widely used in medical devices and chemical equipment because of their excellent corrosion resistance. For example, 316L stainless steel is more resistant to corrosion than 304 stainless steel in corrosive environments and is commonly used in marine equipment. Titanium, on the other hand, is resistant to salt water corrosion and is an ideal material for submersibles and deep-sea probes.
4. Plasticity and ductility
Metal materials usually have good ductility, easy to process complex shapes. Brass has excellent ductility and is easy to cut after machining, making it suitable for the manufacture of precision components. In CNC machining, metals with higher ductility not only reduce tool wear, but also improve the stability of the finished product and save machining time.
5. High temperature stability
Metals such as titanium and stainless steel can maintain good mechanical properties at high temperatures and are therefore widely used in aerospace applications. For example, Ti-6Al-4V titanium alloy can be used in environments up to 400 ℃ without significant deformation. The properties of such materials are particularly critical in the manufacture of high-temperature engine components and spacecraft parts.
Second, the application areas and cases of common metal materials
1. Aluminum
Aluminum is lightweight, moderately strong, has excellent corrosion resistance and thermal conductivity, commonly used in aerospace, automotive parts and electronic product shells. For example, Boeing uses a variety of aluminum alloy materials in its 787 Dreamliner, making the aircraft about 20% lighter than traditional models and improving fuel efficiency. In CNC machining, the excellent machinability of aluminum material is manifested in shorter machining time and higher cutting accuracy.
2. Stainless steel
Stainless steel is corrosion-resistant and strong, which makes it suitable for food equipment, medical equipment, and chemical equipment. For example, scalpels and medical forceps are usually made of 304 stainless steel, while stents and prostheses are made of the more corrosion-resistant 316L stainless steel. In CNC machining, stainless steel materials can maintain high surface quality, especially for precision medical devices and connectors.
3. Copper
Copper has excellent electrical and thermal conductivity and occupies an important position in the electrical and electronic industry. For example, heatsinks, a key component in 5G base stations, are made of copper because of its high thermal conductivity of 401 W/(m-K). In CNC machining, copper material has a good surface finish after machining, but the machining process needs to strictly control the cutting force to avoid burrs affecting the quality of the finished product.
4. Titanium
Titanium is widely used in aerospace, medical and chemical equipment for its high strength, corrosion resistance and light weight. For example, SpaceX’s Falcon rocket uses a large number of titanium parts to maintain stability in alternating high and low temperature environments. CNC machining of titanium is difficult, but under tightly controlled cooling conditions, the finished product is extremely accurate and durable, making it suitable for products such as surgical implants and aircraft components that have stringent requirements for strength and accuracy.
5. Brass
Brass’s corrosion resistance and ease of machining make it widely used in instrumentation parts, electronic parts and decorative applications. For example, many high-end audio connection plugs use brass for excellent electrical conductivity. In CNC machining, brass material has good cutting performance, shorter machining time and high surface finish, which is ideal for producing durable connectors and precision structural parts.
Third, the performance of metal materials in CNC machining
Different metal materials in CNC machining performance varies, the following specific data to illustrate the processing characteristics of various types of metals.
1. Aluminum
Aluminum in CNC machining cutting speed, smooth surface, good heat dissipation. For example, the cutting speed of aluminum can reach 600 m/min, nearly three times faster than stainless steel, shorter processing time and high precision, suitable for efficient mass production. Apple uses aluminum alloy to manufacture its MacBook shell, which has excellent finish and hardness after CNC machining.
2. Stainless steel
Stainless steel has high hardness and is suitable for cutting, but the thermal conductivity is general, and proper cooling is required during machining. For example, 316L stainless steel requires low-speed machining, with a cutting speed generally below 30 m/min to avoid material deformation caused by elevated temperature. Its finished product surface quality is high, is the ideal material for precision medical equipment, food processing equipment.
3. Copper
Copper has excellent thermal conductivity and high surface finish after CNC machining, but the material is soft and prone to burrs. Generally in 100-200 m/min cutting speed can obtain good processing results, in the electronic contact parts, heat sinks and other precision parts are widely used.
4. Titanium
Titanium material CNC machining requires low-speed cutting, general cutting speed of 30 m/min or less, processing difficulty is higher, but the stability of the finished product is excellent. Boeing 787 wing connectors are made of titanium alloy to cope with the high-frequency vibration environment during takeoff and landing, and the machining accuracy reaches ±0.01 mm.
5. Brass
Brass in the CNC machining performance is very good, cutting speed of up to 300 m / min, the finished product surface finish is very high. Many clocks and instrument components are made of brass, which ensures the aesthetics and precision of the products.
The performance and application characteristics of different metal materials in CNC machining are distinctive. Practical data and case studies show that aluminum, copper, stainless steel, titanium and brass all have unique advantages in terms of strength, durability, thermal conductivity and machinability. Understanding these properties can help in selecting the right material for a specific application, ensuring that the finished CNC-machined product meets specific functional, quality and cost requirements. Proper material selection and process control can significantly improve machining efficiency and finished product quality, enabling CNC machining companies to better meet customer needs.