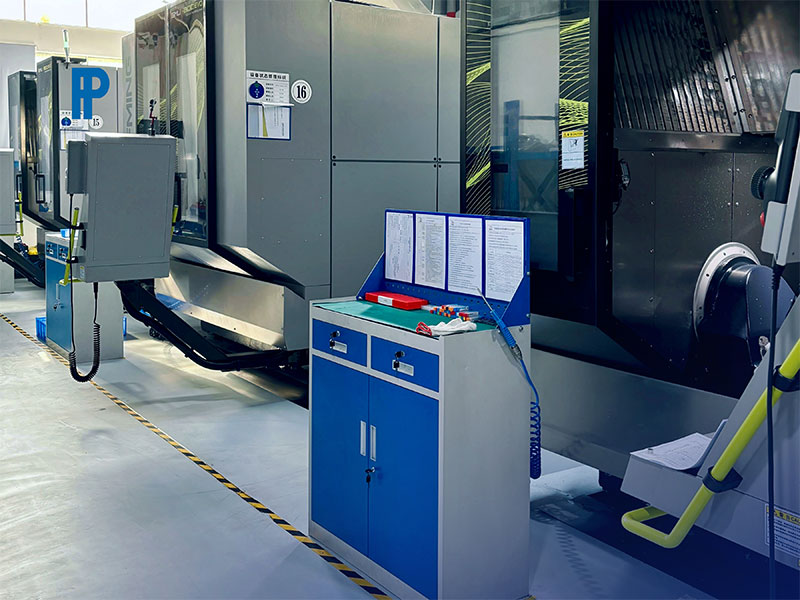
What is CNC machining
CNC machining is a technology that uses computer-controlled machine tools to precisely machine complex workpieces. Compared to traditional manual or semi-automated machining, CNC machining is best characterized by its full automation and high precision, which drives the movement of the machine tool through CNC codes (G-code and M-code, etc.) to accurately cut, mill, drill, or turn a variety of materials.
CNC machining can be used on a variety of materials such as metals, plastics, composites and ceramics. It is suitable for a wide range of applications from small precision parts to large structural components.
Technical Principles of CNC Machining
The basic principle of CNC machining is the use of a computer for control, which performs continuous cutting operations on the workpiece according to a pre-written program. Below we break down its main technical steps:
1. Design and Programming
CAD/CAM Software Design: All CNC machining processes begin with Computer Aided Design (CAD). In this step, FP’s engineers use specialized software to create 3D models and drawings to design the exact shape and dimensions that the customer needs to machine.
CNC Programming: After the CAD design is complete, computer-aided manufacturing (CAM) software is used to convert the design into CNC code. This code instructions include tool paths, cutting speeds, feed rates, etc. With these parameters, the CNC machine is able to know exactly how to machine the material.
2. Setup and Calibration
Material Clamping: At FastPreci, we select the right material for the customer’s specific needs and then secure it to the machine to ensure that the material does not move or deflect throughout the machining process.
Tool selection and calibration: We select the right tool for each material and the accuracy required by the customer. Before each machining session, FastPreci’s technicians calibrate the tools to ensure that each tool maintains consistent accuracy during the cutting process.
3. Cutting and Machining
Fully Automated Machining: When everything is ready, the CNC machine begins fully automated operation, where the cutting process is carried out by controlling the path of the tool and the feed rate. the CNC machine cuts and polishes the material with a high degree of precision under the direction of the CNC system.
Multi-Axis Machining: FastPreci’s CNC machines are equipped with 3-, 4-, and even 5-axis linkage capabilities, which allow us to machine complex 3-D surfaces and structures. For example, in the machining of aerospace parts, five-axis linkage allows us to machine from multiple angles in one pass, avoiding multiple setups and repositioning, thus improving accuracy and efficiency.
4. Quality control and inspection
Real-time monitoring and adjustment: FastPreci is equipped with a real-time monitoring system during the machining process, capable of detecting temperature, vibration and other data during machining to ensure tool wear and machining stability.
Final Inspection: After machining is complete, we use high-precision Coordinate Measuring Machines (CMMs) and other equipment to inspect the quality of the finished product to ensure that each part meets the customer’s requirements for dimensions, surface finish, and shape tolerances.
Complexity and Challenges of CNC Machining
The complexity of CNC machining is not only reflected in the sophistication of the equipment, but also in the comprehensive synergy of material properties, tool selection, program design, etc. Challenges faced by FP include:
Difficulty of cutting different materials: for example, cutting stainless steel and aluminum have completely different strategies. Highly hard materials require stronger tools and lower feed rates, while softer materials require fast cutting to avoid overheating and deformation of the material.
Requirements for micron-level accuracy: In precision machining, FastPreci’s equipment can achieve tolerance control of up to ±0.01mm, a level of accuracy that is especially important in high-precision industries such as medical devices and electronic parts.
CNC Machining Examples
FP has manufactured high-precision stainless steel parts with extremely tight tolerances for a medical device company. For this project, we used 5-axis CNC machining equipment, combined with efficient programming and process design, to complete complex 3D surface machining in a short period of time. Through the precise control and tuning by the FastPreci team, the dimensional accuracy of the final product was controlled within ±0.005mm, exceeding the customer’s expectations.
In another project, we machined a batch of aluminum alloy structural parts for an automotive parts supplier, utilizing a 4-axis CNC machine to complete precise cuts at several different angles, ensuring the dimensional accuracy and shape tolerance of each part in different directions.
The precision and efficiency of CNC machining comes from advanced technological principles and equipment control, and this complex manufacturing process is the cornerstone of high-quality production in modern industry. Through specialized CNC technology and strict quality control, FP ensures high standard machining solutions for our customers. Whether it’s aerospace, medical devices, or automotive components, we have the ability to meet your needs and realize your innovative designs.