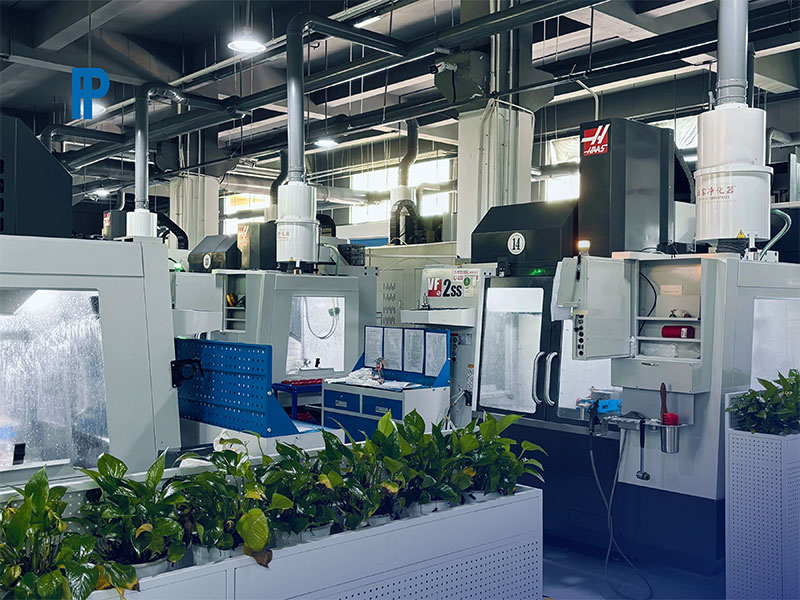
Step 1: Design and Requirements Analysis
The first step in the CNC machining process is a detailed requirements analysis and product design. Customers often provide detailed specifications, including dimensions, materials, surface finishes, and functional requirements, and FastPreci’s engineering team works closely with the customer to ensure that all requirements are accurately understood.
- Case in point: A customer needed to manufacture complex heat sink parts for electronic devices. Through requirements analysis, FP’s design team decided to use aluminum alloy as the material and optimized the design to improve heat dissipation efficiency and reduce weight.
- Data support: Studies show that about 70% of part design changes are due to inadequate early communication. fp significantly reduced this risk through in-depth requirements analysis, ensuring that the design met machining requirements from the start.
Step 2: CAD Design and CAM Programming
Once the design is confirmed, engineers use computer-aided design (CAD) software to generate a 3D model. The accuracy of this stage directly determines the quality of the subsequent machining. once the CAD model has been created, the CAM (Computer Aided Manufacturing) software is responsible for generating the CNC program, which is converted into G-code that guides the CNC machine’s cutting path.
- FastPreci Professional Perspective: FastPreci utilizes the latest CAD/CAM technology to ensure that every detail of the part is precisely realized. Our programming team develops optimal machining solutions to maximize machining efficiency and accuracy based on part complexity, material properties, and tolerance requirements.
- Case in point: FastPreci manufactured highly complex implants for a medical device company, and after multiple programming optimizations ensured optimal efficiency of the machining path, resulting in a 20% reduction in machining time.
Step 3: CNC machining – the heart of precision cutting
The CNC machine starts the machining task, which is the core step of the process.FP has a multi-axis CNC machine capable of performing a wide range of machining operations such as milling, turning, drilling and tapping. This versatility allows FastPreci to machine everything from simple parts to complex geometries.
- Machining Control: Cutting speeds, feed rates, and tool selection are key factors in the quality of a part, and FastPreci’s technicians are experienced in adapting machining parameters to different materials and geometries to achieve optimal surface quality and dimensional accuracy.
- Data support: Statistically, up to 85% of machining errors are due to tool wear or improper selection of cutting parameters. fastPreci significantly reduces machining errors by using high quality tools and real-time monitoring technology.
Step 4: Quality Inspection and Accuracy Control
After CNC machining is complete, quality inspection is an essential step, and FastPreci utilizes precision measuring instruments, such as Coordinate Measuring Machines (CMMs) and laser measurement equipment, to ensure that the part meets the customer’s tolerances and surface finish requirements.
Case in point: FastPreci has machined a batch of complex driveline parts for a customer in the automotive industry, with very tight tolerances on each part. Through CMM inspection and process optimization, our delivered parts were 100% compliant with the requirements and won high praise from the customer.
Step 5: Surface treatment and subsequent processing
According to customer requirements, FastPreci also provides various surface treatment processes, such as anodizing, plating, spraying, etc., to enhance the corrosion resistance, wear resistance and appearance quality of the parts.FastPreci will recommend the most suitable surface treatment program according to the use of the parts.
Example: An aerospace customer required a part with high temperature and corrosion resistance, and FastPreci’s anodizing treatment increased the service life of the part by 30%.
Step 6: Delivery and After-Sales Service
Once machined, FastPreci ensures that the part is well packaged and delivered on time. Our rapid delivery mechanism and flexible logistics support ensure that projects are completed on schedule. At the same time, FastPreci provides customers with comprehensive after-sales support to ensure that the machined parts perform well in real-world applications.
Supporting data: Over the past year, FastPreci has achieved an on-time delivery rate of 98%, which is significantly higher than the industry average. Efficient process management allows our customers to always have confidence in delivery times.
Conclusion: A professional CNC machining process that drives your project success
The CNC machining process is a highly integrated, complex process from design to delivery, and FastPreci Precision Manufacturing ensures that each project meets our customers’ high standards through accurate requirements analysis, advanced programming techniques, precision machining equipment, and rigorous quality control processes.