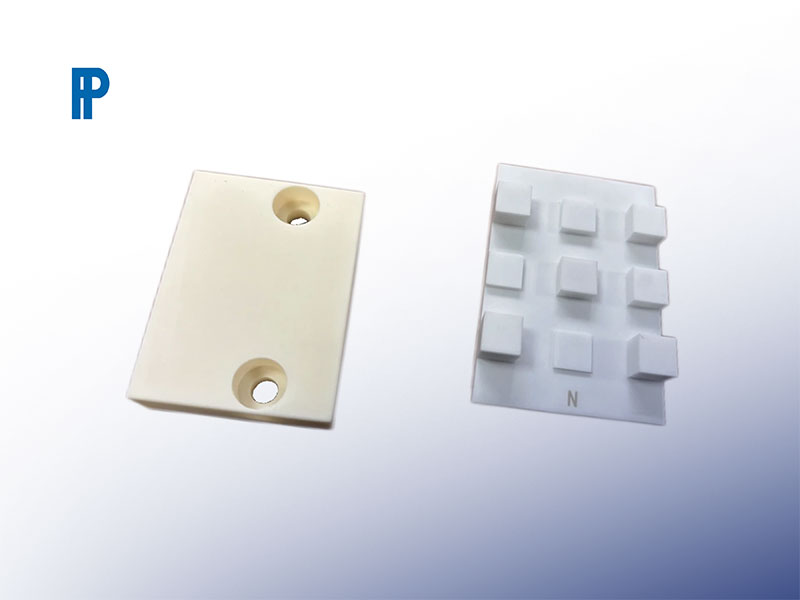
First, the characteristics of ceramic materials
1. Extremely high hardness
The hardness of ceramics is extremely high, the Mohs hardness reaches 8 to 9, second only to diamond. This high hardness makes ceramic materials resistant to extreme mechanical wear and is suitable for the manufacture of high-strength and highly wear-resistant components. For example, zirconia ceramics have a hardness of up to 1,200 HV and excel in complex mechanical components.
2. High temperature resistance
Ceramic materials can remain stable at high temperatures and are highly heat resistant. For example, the melting point of alumina ceramics is as high as 2000℃, much higher than metal materials. It is not easy to soften and deform in extremely high temperature environments, making it an ideal material for aerospace engine components and other fields.
3. Corrosion resistance and chemical stability
Ceramic materials have good corrosion resistance to acids, alkalis and most chemical reagents, especially silicon nitride ceramics, which are widely used in chemical pumps, valves and seals and other equipment exposed to corrosive media for a long time.
4. Low density and low conductivity
Ceramic materials with low density and light weight, such as silicon nitride ceramic density of 3.2g/cm³, about 40% lighter than steel. In addition, most of the low conductivity of ceramics, suitable for use as insulating materials in electronic devices.
Second, the application areas of ceramic materials
1. Electronics and semiconductors
The electrical insulation of ceramic materials makes them one of the basic materials for the manufacture of electronic components and semiconductors. Alumina ceramics are commonly used in the manufacture of circuit substrates, aluminum nitride ceramics are used for high-power LED heat sinks. Data show that the thermal conductivity of aluminum nitride ceramics reaches 170W/(m-K), ten times that of traditional silicon materials, effectively solving the problem of heat dissipation in power devices.
2. Aerospace
Silicon nitride ceramics are widely used in jet engine blades and turbine components because of their high temperature resistance and lightweight characteristics. For example, GE Aviation has used gas turbine blades made of silicon nitride ceramics on its engines, increasing engine efficiency by about 5%.
3. Medical field
Zirconia ceramics are widely used in medical implants and dental restorative materials due to their biocompatibility and anti-wear properties. For example, zirconia ceramic implants in dental restorations last twice as long as conventional materials while reducing the risk of allergic reactions.
4. Industrial components
The hardness and wear resistance of alumina ceramics make them widely used in cutting tools and molds. Ceramic cutting tools are more efficient in processing metal materials such as steel and iron due to their high hardness and high temperature resistance, and their service life is five times longer than traditional tools.
Third, ceramic materials in CNC machining performance
Ceramic materials in CNC machining performance, but also because of its high hardness, brittle and face certain processing difficulties. The following are several common ceramic materials in CNC machining specific performance and practical application cases.
1. Alumina ceramics
The hardness and toughness of alumina ceramics in the cutting and grinding process is excellent, but the cutting tool has high requirements. In CNC machining, diamond tools are usually used to ensure cutting accuracy and surface finish. For example, a mechatronic company uses CNC machining cutting tools made of alumina ceramics, and the surface roughness is controlled below Ra0.2μm, which greatly improves the precision and aesthetics of the machined parts.
2. Silicon nitride ceramics
Silicon nitride ceramics have superior stability under high-temperature conditions and are suitable for machining high-temperature parts. In CNC machining, ultra-high-temperature cooling is often used to prevent the ceramic from becoming brittle. GE Aviation has performed CNC finishing on blades made of silicon nitride ceramics, and has successfully produced high-temperature-resistant, impact-resistant blades under strict temperature control, which has significantly improved the fuel efficiency of the engine.
3. Zirconia Ceramics
Zirconia ceramics are widely used in the manufacture of high-precision medical devices and surgical knives due to their excellent crack and wear resistance. In CNC machining, zirconia ceramic tools use fine grinding technology to obtain extremely high surface quality. Taking dental implants as an example, the surface roughness of zirconia ceramic implants reaches Ra 0.05 μm, ensuring good biocompatibility and wear resistance.
Typical processes and challenges in the processing of ceramic materials
1. Precision grinding process
CNC machining of ceramics mainly adopts precision grinding, due to the brittle nature of ceramic materials, the depth of cut needs to be controlled to prevent the material from chipping. The general precision of grinding process can reach below ±0.01mm, which is suitable for high precision medical and electronic devices.
2. Laser cutting and EDM
For ceramic materials with small thickness, laser cutting and EDM is a more efficient method. A microelectronics company uses laser cutting technology to process alumina ceramics into miniature circuit boards with an accuracy of ± 0.005 mm, effectively improving the stability and durability of components.
3. Cooling and lubrication control
Ceramic processing due to its low thermal conductivity is prone to high temperatures, generally using coolant for forced cooling. In the case of silicon nitride, for example, liquid nitrogen is usually used for cooling to avoid thermal expansion and brittle damage and to improve the surface finish and dimensional accuracy of the finished product.
Ceramic materials are widely used in electronics, aerospace, medical and other demanding industries due to their excellent hardness, high temperature and corrosion resistance. In CNC machining, ceramic materials are able to demonstrate outstanding performance in the manufacture of high-precision and high-durability products through precise control of process, cooling technology and tool selection. Proper use of ceramic materials can bring customers more performance advantages and provide more high-performance solutions for the manufacturing industry.