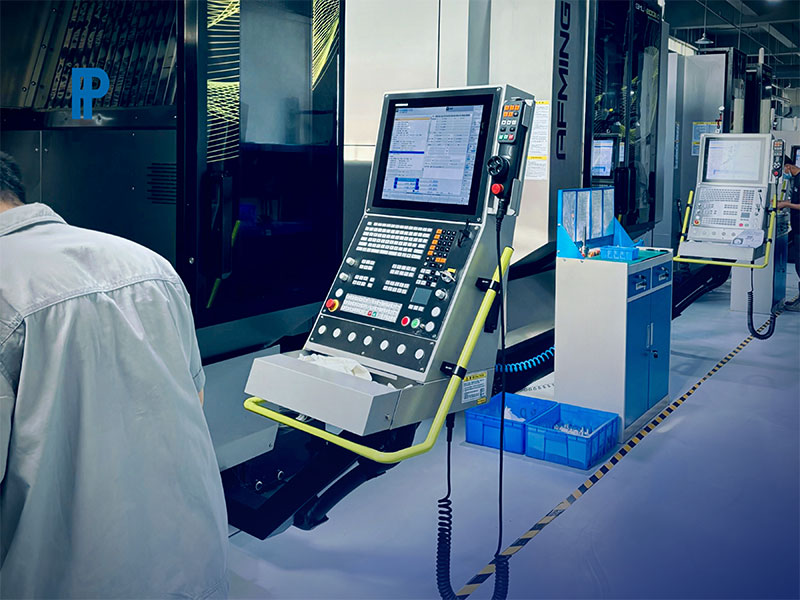
1. Optimize material selection to reduce raw material costs
In CNC machining, material costs typically represent a significant portion of the total project cost. By carefully analyzing project requirements, FastPreci helps customers select more cost-effective materials. For example, for wear resistance needs, ABS plastic may be more economical than other high-end materials such as PEEK. At the same time, using alternative materials with the same mechanical properties but at a lower price can be an effective way to reduce material costs.
Case study: An automotive parts manufacturer needed to produce a batch of heat-resistant parts, and initially chose PEEK. However, FastPreci was able to reduce material costs by 30% by recommending that the customer switch to PC, which has similar heat resistance, through a comparison of properties.
2. Improved machining efficiency, reduced labor hours and machine wear and tear
FastPreci uses advanced equipment and processes to improve productivity during CNC machining. By optimizing machining paths and rationalizing machining sequences, unnecessary man-hours and machine wear can be reduced, thus saving customers’ costs. For example, multi-axis machining technology allows multiple angles of cut to be clamped at once, reducing the number of tool changes and repositioning and greatly increasing productivity.
Supporting data: FastPreci has reduced machining time by 20% through its multi-axis machining program, resulting in a 15% savings in production costs.
3. Reducing waste and fine-tuning inventory management
Machining waste is also a major source of cost, and FP reduces material waste through accurate machining program design and efficient scrap handling systems. In the design proposal provided by the customer, FastPreci engineers use numerical simulation to predict the possible material waste points in the machining process in advance and make optimized design to reduce unnecessary material waste.
Case study: When a medical device company cooperated with FastPreci, it reduced the waste rate from 10% to less than 2% through precise CNC solutions, saving a lot of material costs.
4. Reduce labor and quality control costs by applying automation and intelligent technologies
FastPreci has widely applied automation technology in CNC machining, such as robot operation and intelligent control system. This not only reduces the dependence on manual operation, but also improves the accuracy of quality control through automatic inspection. The intelligent quality control system ensures that each part meets the customer’s requirements, resulting in reduced rework and scrap rates, and further cost savings.
Quote: By introducing an automated inspection system, FastPreci has reduced rework by approximately 25% and improved overall productivity.
In CNC machining projects, controlling costs is not just about choosing cheaper materials or equipment, but requires a comprehensive consideration of materials, processes, management, etc. With years of experience in the industry and accumulation of technology, FastPreci helps customers to optimize costs while maintaining quality. If you want your project to be completed efficiently and at a controlled cost, FastPreci is your reliable partner.
By analyzing all aspects of cost control, FastPreci not only saves money, but also ensures product quality and delivery time. When you choose FastPreci, you choose professionalism, efficiency and success.