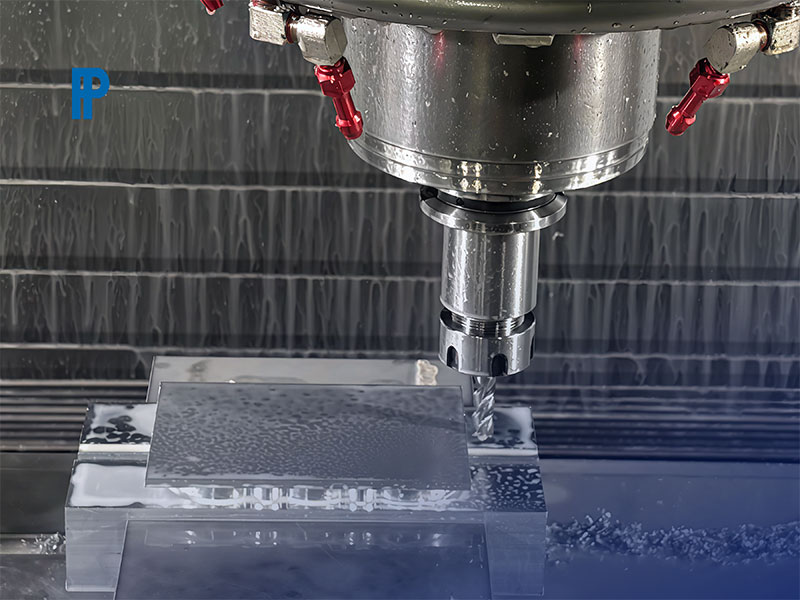
1. Accurate Planning and Design: Reducing Upfront Errors
When FastPreci receives a project request from a customer, the first step is to conduct detailed project planning and design. This includes not only 3D modeling and CAD design of the product, but also the use of advanced software to simulate the process, so as to ensure that any problems that may arise can be detected and solved before the official production.
For example, in a project for an electronic device housing, we identified potential cutting errors through simulation and adjusted tool paths in advance, ultimately improving machining efficiency by 15%.
2. Intelligent management of machining equipment: improving productivity
FastPreci has introduced advanced intelligent CNC machining equipment with automated calibration functions and real-time monitoring capabilities. By integrating Industrial Internet of Things (IIoT) technology, our equipment continuously monitors parameters such as temperature, vibration, and cutting forces during machining to ensure machining accuracy and material quality.
For example, in the production of a medical device component, after using intelligent management, the equipment was able to automatically adjust the machining parameters, reducing the scrap rate and increasing productivity by 20%.
3. Optimized tool paths and machining strategies: reduced machining time
By optimizing toolpaths, FastPreci was able to significantly reduce CNC machining time. We select the best cutting paths and feed rates based on material properties and part geometry to improve machining efficiency and avoid unnecessary downtime.
In one aerospace project, we optimized the machining path of an aluminum alloy structural part, reducing the machining time from 60 hours to 40 hours, while ensuring high accuracy and surface finish of the product.
4. Production Monitoring and Quality Control: Ensuring Product Consistency
FastPreci implements strict quality control at every step of the production process to ensure that every machined part meets the customer’s requirements. We utilize CMMs (Coordinate Measuring Machines) to perform precision inspections of finished products, as well as record every parameter of the machining process to ensure product consistency and reliability.
FastPreci’s quality control system has helped us reduce rework by 30% on one automotive part, resulting in significant cost savings and improved lead times.
5. Ongoing communication and feedback with customers: Ensuring demand matching
In addition to optimizing the production process, we also focus on communicating with our customers, and FastPreci assigns a dedicated account manager to each project to ensure that we are aware of our customers’ needs and feedback during the production process. Through continuous communication with our customers, we are able to quickly adjust our production solutions to better meet their individual needs.
In a project in the electronics industry, we adjusted the product design requirements midway through the project through close communication with the customer, and the final delivery not only met the new specifications, but also advanced the delivery date.
Through continuous optimization of production processes, introduction of intelligent equipment, precise quality control, and close cooperation with our customers, FP is able to provide more efficient and reliable CNC machining services to our customers. Our goal is not only to help our customers save time and cost, but also to demonstrate professionalism in every detail to ensure that our customers get the best machining experience.
As a company dedicated to efficient and precise CNC machining, FastPreci is always innovating and optimizing its technology and processes. Choosing FastPreci means choosing a team that is constantly improving efficiency and pursuing excellence.