Custom Plastic CNC Machining
FastPreci offers a wide range of high-quality engineering plastics, including ABS, POM, PMMA, PVC, nylon, PC and PEEK, to meet the needs of multiple fields such as electronics, automotive, medical and industrial. Dedicated to providing durable and precise plastic solutions.
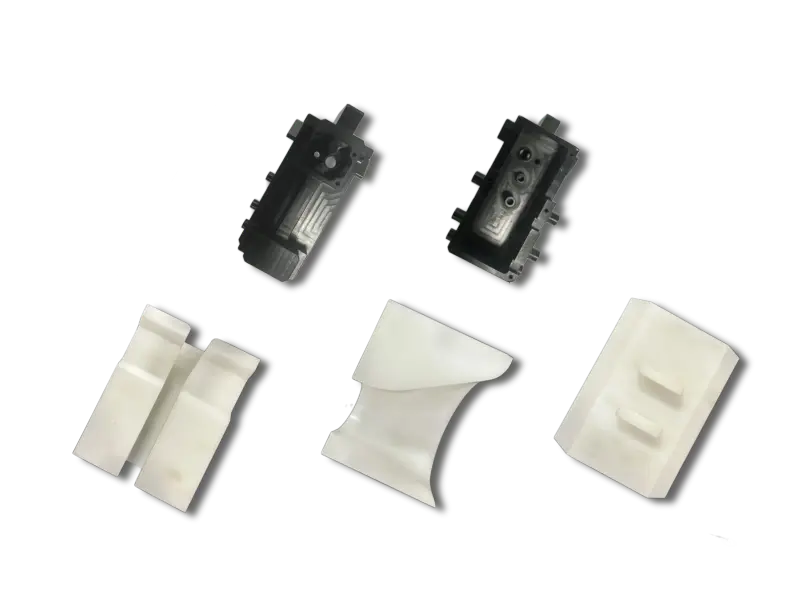
Commonly Used Plastic Materials
ABS material (acrylonitrile-butadiene-styrene) is suitable for the manufacture of complex geometric parts due to its excellent mechanical properties, impact resistance, toughness, and heat resistance.ABS material is easy to cut, has a smooth surface, and is easy to color and paint, and is commonly used in automotive parts, electronic housings, and home appliances. Its insulating properties also make it suitable for electrical equipment.
Model | Density (g/cm³) | Tensile strength (MPa) | Modulus of elasticity (MPa) | Heat deflection temperature (°C) | Impact strength (kJ/m²) | Hardness (Rockwell) |
ABS standard grade | 1.04-1.06 | 35-45 | 1500-2000 | 85-100 | 15-30 | R80-R100 |
ABS Flame Retardant Grade | 1.08-1.10 | 30-40 | 1400-1900 | 80-95 | 10-20 | R80-R95 |
ABS Enhanced Grade | 1.10-1.15 | 40-50 | 1800-2200 | 90-105 | 20-30 | R85-R100 |
ABS weathering grade | 1.05-1.07 | 30-40 | 1600-1900 | 75-90 | 10-25 | R80-R90 |
POM material (polyoxymethylene), also known as cysteel or derrin, is often used for high-precision parts in CNC machining because of its high strength, wear resistance, low coefficient of friction and dimensional stability. It is suitable for the manufacture of mechanical parts such as gears, bearings, pulleys and valves, and has good fatigue and chemical resistance, and can be used in a wide range of temperatures.POM materials are widely used in automobiles, electronics, industrial equipment and other parts that require high precision and longevity to be processed.
Model | Density (g/cm³) | Tensile strength (MPa) | Modulus of elasticity (MPa) | Heat deflection temperature (°C) | Coefficient of friction | Hardness (Rockwell) |
POM-C(Copolymerization) | 1.41-1.43 | 60-70 | 2400-2800 | 110-120 | 0.2-0.3 | R80-R85 |
POM-H (homopolymer) | 1.42-1.43 | 70-80 | 2900-3100 | 120-130 | 0.2-0.25 | R85-R90 |
POMGF (glass fiber reinforced) | 1.55-1.60 | 85-100 | 4500-5000 | 130-140 | 0.25-0.3 | R90-R95 |
POM high wear-resistant grade | 1.43-1.45 | 60-70 | 2400-2800 | 110-120 | 0.1-0.2 | R80-R85 |
PMMA material (polymethyl methacrylate), commonly known as acrylic or Plexiglas, is widely used in optical lenses, display panels, lampshades, and other high-transparency applications due to its excellent transparency (light transmission rate of up to 92%), weathering resistance, and processability.PMMA is characterized by its high hardness, scratch-resistance, and light weight, making it suitable for electronics, automotive, medical equipment, and architectural decoration, and meeting the demands for aesthetics, durability, and light weight. It is suitable for electronics, automotive, medical equipment and architectural decoration fields to meet the needs of aesthetic, durability and light weight.
Model | Density (g/cm³) | Tensile strength (MPa) | Modulus of elasticity (MPa) | Heat deflection temperature (°C) | Optical transmittance (%) | Hardness (Rockwell) |
PMMA-Cast | 1.19-1.20 | 60-70 | 3000-3300 | 85-100 | 92-93 | R90-R105 |
PMMA-Extruded | 1.18-1.19 | 50-65 | 2800-3000 | 80-95 | 90-92 | R85-R95 |
PMMA High Impact | 1.18-1.20 | 55-65 | 2800-3100 | 80-95 | 89-91 | R85-R100 |
PMMAUV Stabilized | 1.19-1.20 | 60-70 | 3000-3300 | 85-100 | 90-92 | R90-R105 |
PVC material (polyvinyl chloride) is widely used in corrosion-resistant demand scenarios such as piping, valves, and chemical equipment due to its excellent chemical resistance, mechanical strength, and low cost.PVC possesses good processability, insulation, and flame-retardant properties that make it suitable for use in the electrical and electronics industries, and it is the ideal choice for cost-effective use in the chemical, construction, and water treatment sectors.
Model | Density (g/cm³) | Tensile strength (MPa) | Modulus of elasticity (MPa) | Heat deflection temperature (°C) | Hardness (Rockwell) | Water absorption (%) |
PVC-U (Rigid PVC) | 1.38-1.42 | 45-55 | 2500-3000 | 70-80 | 80-85 | 0.04 |
PVC-C (Chlorinated PVC) | 1.50-1.60 | 48-58 | 2200-2600 | 100-105 | 80-86 | 0.05 |
PVC-P(Soft PVC) | 1.20-1.35 | 15-25 | 1500-2000 | 50-60 | 50-60 | 0.2 |
PVC-ESD(Anti-static) | 1.40-1.45 | 45-55 | 2500-3000 | 70-80 | 80-85 | 0.04 |
HDPE material (High Density Polyethylene) is widely used in CNC machining due to its excellent chemical resistance, impact resistance, low water absorption and abrasion resistance. Its toughness and low density make it suitable for lightweight, high-strength parts, especially in corrosion-resistant scenarios such as chemical, food processing, and water treatment, etc. HDPE is easy to process and is suitable for tanks, pipeline linings, gears, and sliding parts, etc., and is a highly effective engineering plastic due to its combination of abrasion resistance and low friction properties.
Model | Density (g/cm³) | Tensile strength (MPa) | Modulus of elasticity (MPa) | Heat deflection temperature (°C) | Hardness (Rockwell) | Water absorption (%) |
HDPE300 | 0.94-0.96 | 20-30 | 800-1000 | 50-60 | 60-65 | <0.01 |
HDPE500 | 0.94-0.96 | 25-35 | 1000-1200 | 60-70 | 65-70 | <0.01 |
HDPE1000 | 0.94-0.96 | 30-40 | 1200-1400 | 70-80 | 67-70 | <0.01 |
HDPEUV-Stabilized | 0.94-0.96 | 25-35 | 1000-1200 | 60-70 | 65-70 | <0.01 |
Nylon material (nylon or polyamide) is widely used in CNC machining due to its excellent wear resistance, high tensile strength, toughness and low coefficient of friction. Its mechanical strength and durability make it suitable for highly durable, impact-resistant parts. nylon’s chemical resistance, low water absorption, shape stability, low friction and self-lubricating properties also make it suitable for sliding parts such as gears, bearings, and slides, making it ideal for wear-resistant and durable parts in industrial, automotive, and electronic applications.
Model | Density (g/cm³) | Tensile strength (MPa) | Modulus of elasticity (MPa) | Heat deflection temperature (°C) | Hardness (Rockwell) | Water absorption (%) | coefficient of friction |
Nylon6 | 1.13-1.15 | 70-85 | 2000-2500 | 90-95 | 70-80 | 1.2-1.4 | 0.2-0.25 |
Nylon66 | 1.14-1.16 | 80-90 | 2500-3000 | 100-110 | 75-85 | 1.0-1.2 | 0.2-0.25 |
Nylon12 | 1.01-1.03 | 45-50 | 1500-1800 | 75-85 | 60-70 | 0.3-0.5 | 0.3-0.35 |
Nylon46 | 1.18-1.20 | 90-100 | 3000-3500 | 110-120 | 80-85 | 0.7-0.9 | 0.25 |
NylonMXD6 | 1.21-1.23 | 100-110 | 3200-3500 | 110-120 | 85-90 | 0.5-0.7 | 0.2 |
PC material (polycarbonate) is popular for its impact resistance, transparency, heat resistance and dimensional stability. Its transparent optical properties and high impact strength make it suitable for frequently used parts that require visual effects.PC materials are heat and UV resistant, and are commonly used in high-strength applications such as automotive parts, electronic housings, optical lenses, and protective covers.
Model | Density (g/cm³) | Tensile strength (MPa) | Modulus of elasticity (MPa) | Heat deflection temperature (°C) | Hardness (Rockwell) | Water absorption (%) | Impact strength (kJ/m²) |
PCGeneral | 1.20-1.22 | 60-70 | 2200-2500 | 135-145 | 118-120 | 0.15-0.3 | 60-70 |
PC-ABSAlloy | 1.15-1.18 | 45-55 | 2000-2200 | 110-120 | 110-115 | 0.2-0.4 | 50-65 |
PCFR(Flame retardant) | 1.19-1.21 | 55-65 | 2100-2300 | 125-135 | 117-119 | 0.2-0.3 | 55-65 |
PCUVStabilized | 1.20-1.22 | 60-70 | 2200-2500 | 135-145 | 118-120 | 0.15-0.25 | 60-70 |
PCGFReinforced | 1.30-1.35 | 70-80 | 3000-3500 | 150-160 | 120-122 | 0.1-0.2 | 40-50 |
PEEK (polyether ether ketone) is a high-performance engineering plastic suitable for use in extreme environments due to its resistance to high temperatures (up to 260°C), high strength, chemical resistance, low friction, and biocompatibility.PEEK excels in high-load applications such as bearings, gears, seals, and other mechanical components, as well as in a wide range of applications in the medical, aerospace, and automotive industries.
Model | Density (g/cm³) | Tensile strength (MPa) | Modulus of elasticity (MPa) | Heat deflection temperature (°C) | Hardness (Rockwell) | Water absorption (%) | Impact strength (kJ/m²) |
PEEKNatural | 1.30-1.32 | 90-100 | 3700-4000 | 150-160 | 85-87 | 0.1-0.2 | 40-50 |
PEEKCF30(Carbon fiber reinforced) | 1.40-1.45 | 140-150 | 7000-7500 | 170-180 | 87-90 | 0.05-0.1 | 30-40 |
PEEKGF30(Glass fiber reinforced) | 1.50-1.55 | 110-120 | 6000-6500 | 160-170 | 86-88 | 0.05-0.1 | 35-45 |
PEEKHT(High temperature grade) | 1.31-1.33 | 95-105 | 3800-4200 | 200-220 | 85-87 | 0.1-0.2 | 40-50 |
PEEKMedical | 1.29-1.31 | 90-95 | 3600-3900 | 140-150 | 84-86 | 0.1-0.15 | 38-45 |
Polypropylene (PP) is a commonly used engineering plastic favored in CNC processing for its light weight, chemical resistance, impact resistance, and good processability.PP is suitable for use in acid and alkali resistant, corrosion resistant environments and is widely used in automobiles, electronic equipment, laboratory equipment, and chemical containers. Its low density and good toughness make it suitable for lightweight applications, while maintaining stability in chemical-resistant environments, making it an affordable and versatile plastic material.
Model | Density (g/cm³) | Tensile strength (MPa) | Modulus of elasticity (MPa) | Heat deflection temperature (°C) | Hardness (Rockwell) | Water absorption (%) | Impact strength (kJ/m²) |
PP Homopolymer | 0.90-0.91 | 30-35 | 1400-1700 | 90-100 | 70-75 | <0.05 | 45516 |
PP Copolymer | 0.90-0.92 | 25-30 | 1200-1500 | 70-80 | 65-70 | <0.05 | 12-15 |
PP Glass-Filled | 1.10-1.20 | 40-50 | 3000-3500 | 110-120 | 80-85 | <0.05 | 6-10 |
PP Impact Modified | 0.91-0.92 | 25-28 | 1300-1600 | 60-70 | 65-70 | <0.05 | 15-20 |
- Wide selection to meet application needs.
- Durable and chemical resistant to enhance product life
- High precision machining, customized solutions
- Fast delivery to ensure efficient progress