Precision Casting Services
Precision casting, compared to die casting, has the advantages of low mold costs, complex shapes, tight tolerances, smooth surfaces, less machining, and material savings, providing the most cost-effective solution for mass production of custom parts.
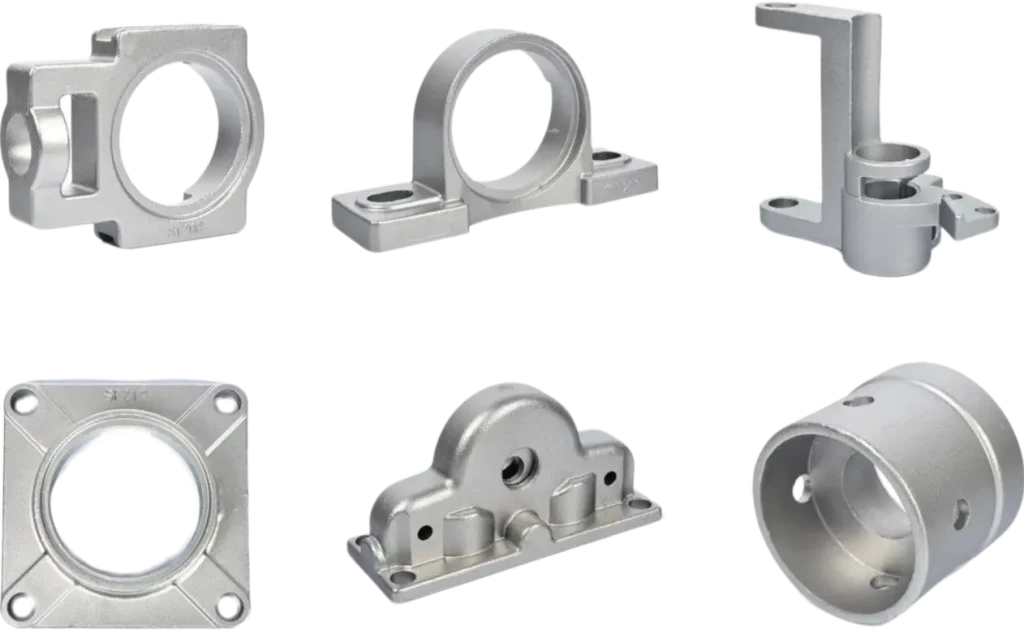
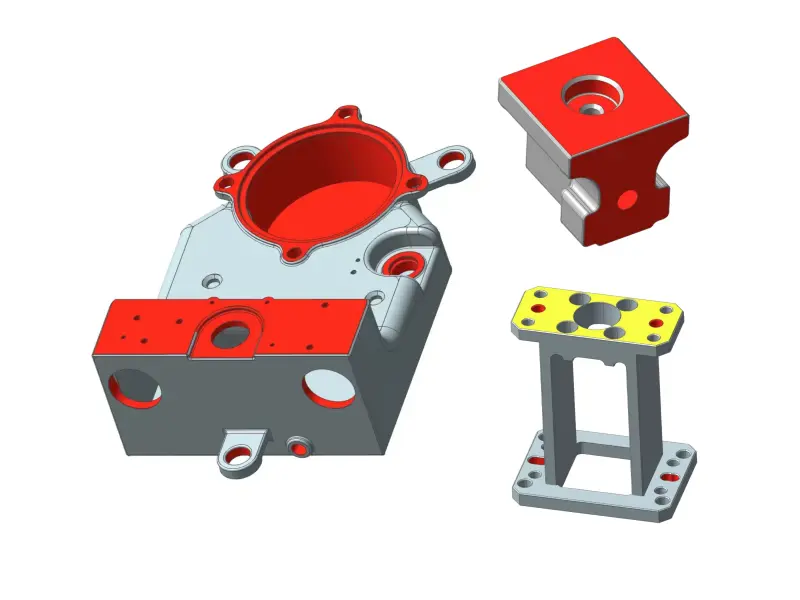
What is Precision Casting?
Precision casting, also known as investment casting or lost wax casting, begins with the creation of a precise wax mold that replicates the required final parts. The wax mold is then coated with a fine ceramic material to form a shell, which is heated to harden the ceramic shell and melt the wax mold, leaving a hollow ceramic mold. The mold is preheated to ensure that the molten metal (usually steel, aluminum or titanium) flows smoothly into the cavity. After the metal has been poured and solidified, the ceramic shell is cracked and the casting is finished. This process ensures excellent detail and dimensional accuracy, making it ideal for manufacturing complex parts with intricate features and tight tolerances, while also significantly saves materials and reduces machining.
FastPreci Precision Casting Capabilities
Lowest | Highest | |||||
Dimension | 10mm | 500mm | ||||
Weight | 10g | 30kg | ||||
Wall Thickness | 1mm | 10mm | ||||
Hole Diameter | 2mm | |||||
Features | 0.5mm | |||||
Linear Tolerance | ±0.1mm | |||||
Angular Tolerance | ±0.5° | |||||
Roughness | Ra3.2 |